使ってくれている人が
ニコッと笑ってもらえるのが
一番うれしい
-開発部 部長 佐久間
開発型企業としての中核を担うのが開発部です。
開発部を統括する佐久間さんの入社時のエピソードなどをご紹介します。
誰かが必要としている、だから作る
「刺子ミシン」という弊社の製品があるのですが、手縫いのような縫い目になるミシンでが、これは世の中でうちしか作っていません。実に特殊な縫い目でして、その当時他にも開発に取り組んでいたメーカーさんもありましたけども、結局製品化できたのは弊社だけなのです。キルトというのが少しブームになり始めた頃でして、2000年代前半だったと思います。
ハンドキルトとミシンキルトの違い
その当時キルトというのは大きく作り方を分けて2種類ありまして、ハンドキルトという手縫いのものと、ミシンキルトという機械縫いのものです。ミシンキルトというのはどちらかと言うとアメリカなんかで使われている実用キルトで、防寒具とかベッドカバーとか日々使うようなものです。
ハンドキルトはどちらかと言うと芸術性を追求するキルトとして認識されていますが、それはやはり、“縫い目”が違うからです。キルトは生地の中に綿を入れるのですが、従来のミシンキルトはでは縫い上がりが“ペタン”としてしまうのです。ハンドキルトは凹凸があって、縫い目の所に少しシワが寄るような温かみを感じるような、ふっくらと独特の風合いが出るのですね。そういう縫い上がりの違いが大きいので、よく知る人ほど「やっぱりハンドキルトだ」ということなのです。
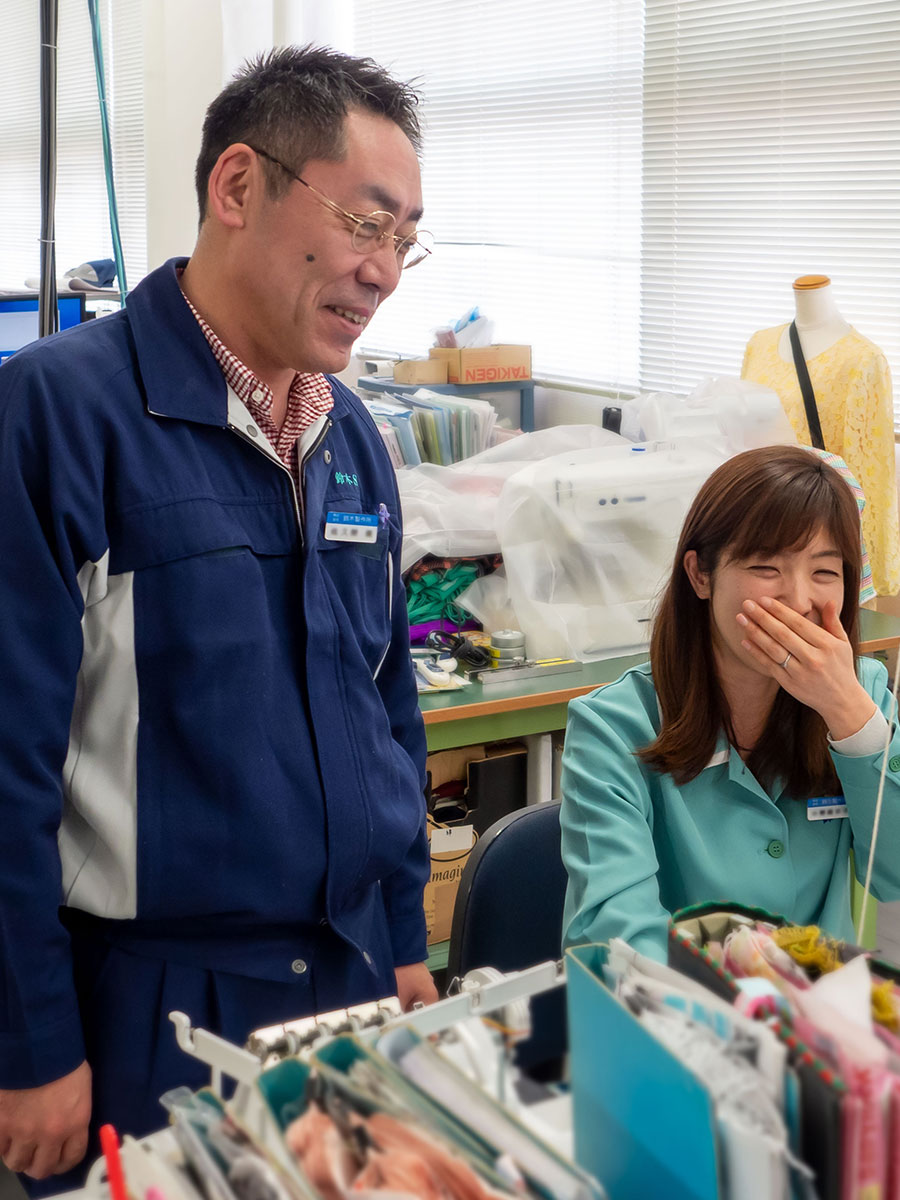
その代償は、大変な腱鞘炎
その立派な大きなハンドキルトの制作者の方々に「本当にこれ全部手縫いですが?」とお聞きすると、大御所の人なんかは「はい、こーんな大きいものも作れますよ!」って得意げにおっしゃられるのですが、ただ手が腱鞘炎になってしまっていて、それがものすごく辛いらしいのです。なので、もしそれをミシンで出来るようになればだいぶ楽になりますよね、ということから開発を始めました。ただ、それまで製品として世の中に出回っていない理由も当然ながらある訳で、おそらく皆さん、作れなかったのですね。その当時のハンドステッチ風に見えるミシンというのもありましたが、透明な糸(釣り糸)を使用している訳でして。その結果、縫い上りはやはりペタンと押さえられた仕上がりになってしまいます。
会社として作る必要があったかと聞かれれば、そうでは無かった
私達が作らなきゃいけなかったという訳ではもちろん無かった訳ですが、当時はキルトも最近ブームになっているしとか、同時に手が痛いっていう人も沢山いるみたいだし、手縫いだと時間もすごいかかって大変だよなぁ・・・と。周囲の知り合いでキルトをやっている人もやっぱり「大変だ大変だ」って言っていて、じゃあちょっとやってみるかと。
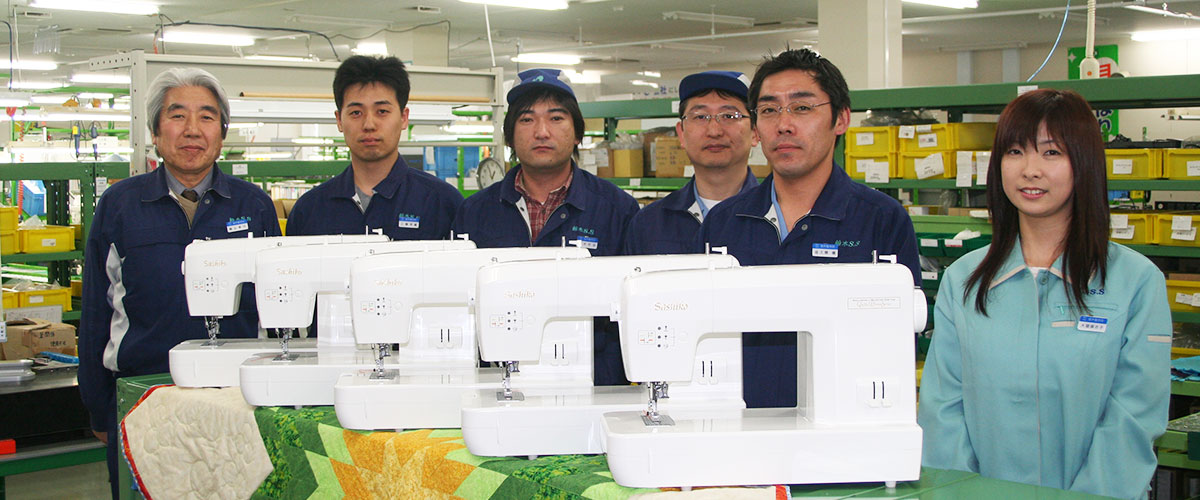
刺子量産開始の記念写真
事前に収支予想なんか立てている訳がない
善し悪しは別として、開発費にいくら必要になりそうかすら試算していなかったですし、どの程度需要がありそうかの予測すらしていないはずです。なんせ類似した手本が他にはない。何が正しいのか全然わからない。そういう暗中模索状態でなんとかやってきていて、でも縫い方も掴んで周辺部品の開発も済んで製品の金型が全部できあがった「もう半年後に発売する」という段階で、一番ミシンの針が動くところの部分をまるっきり右左逆に作ったほうが縫いが安定するってことが最後の最後に判明してしまって・・・。結局発売を一年延ばしてもらって、完成した金型は全部捨てて作り直しをさせてもらって、採算度外視もいいところで・・・。
でも、すごく喜んでいただけています
開発の経緯としては大変でしたが、キルターの方にはすごく喜んでいただけました。今現在も日本のトップキルターの方でご自身でもすごく使っていただいていているのですが、その方のファンの人たちを講習会のような形で2か月に1度集めていただいて、「刺子ミシン研究会」というものを開催してくださっています。「刺子ミシンのもっと楽しい使い方を探しましょう」なんて言って指導してくれたりしています。いやぁ、作ってよかったですよね。
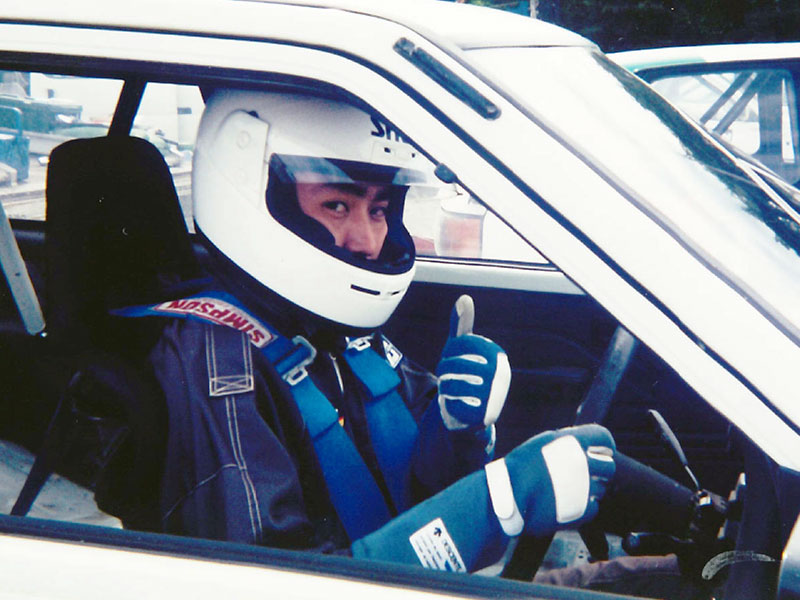
レースに臨む若き日の佐久間さん
中学3年で3級整備士の試験は全問解けた
僕の親父も車が好きで、車に乗せてもらうたびに、「エンジンっていうのはこうなっているんだ」という話を小学校低学年に話すわけです。もう好きになっちゃって、中学校の頃には3級整備士の試験は全問パス。
ダートトライアルというモータースポーツもやっていたことから実際に整備もしていましたし、関東シリーズというレースを走っていました。それでやはり車を作る仕事はしたいなと思っていて、卒業後にエンジン制御の仕事に就きました。
与えられた仕事か、自分で見つけた仕事か
会社に就職してみると、最初は与えられた仕事をこなすだけで精一杯だったのですが、徐々に慣れてくると気持ちに余裕が出てきて、「もうちょっと面白いことやりたいな」っていうような考えが出てきました。一応与件としては「ここまでやればいい」というところがあるのですが、もっと自分が追求したいようであればもっとやっちゃってみて、そうやって自分で自分の仕事を面白くしてたような。それもできるだけ人に頼まないで自分でやっちゃおうみたいなところがあって、実験設備なんかも自分で作ってしまったり、あちこちに勝手に顔を出しては相談したりと、やっぱり意志を持って取り組む技術系の仕事っていうのは楽しいなということを確実に思い始めた頃でした。
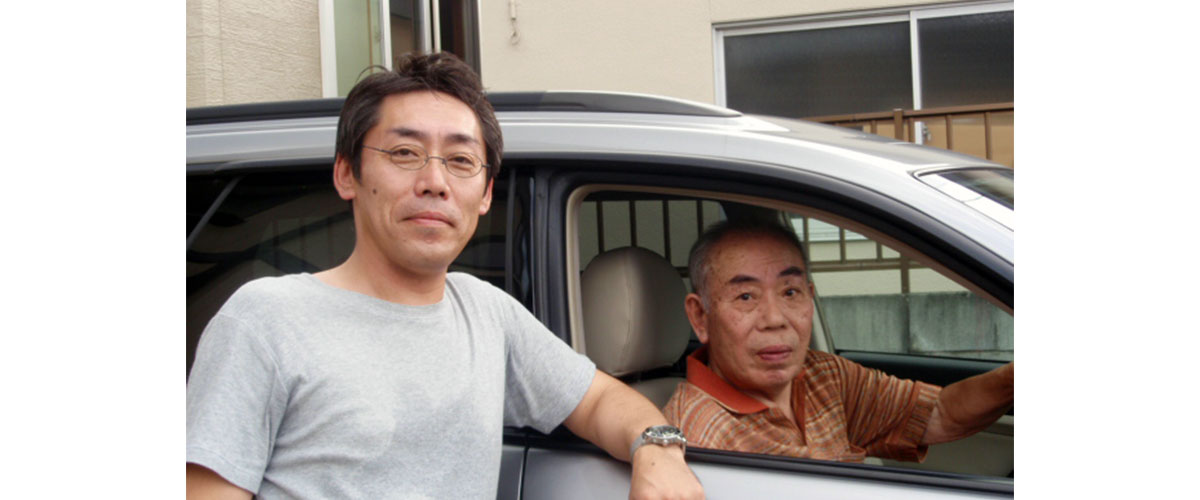
父でありベビーロックの開発者の孝一氏と
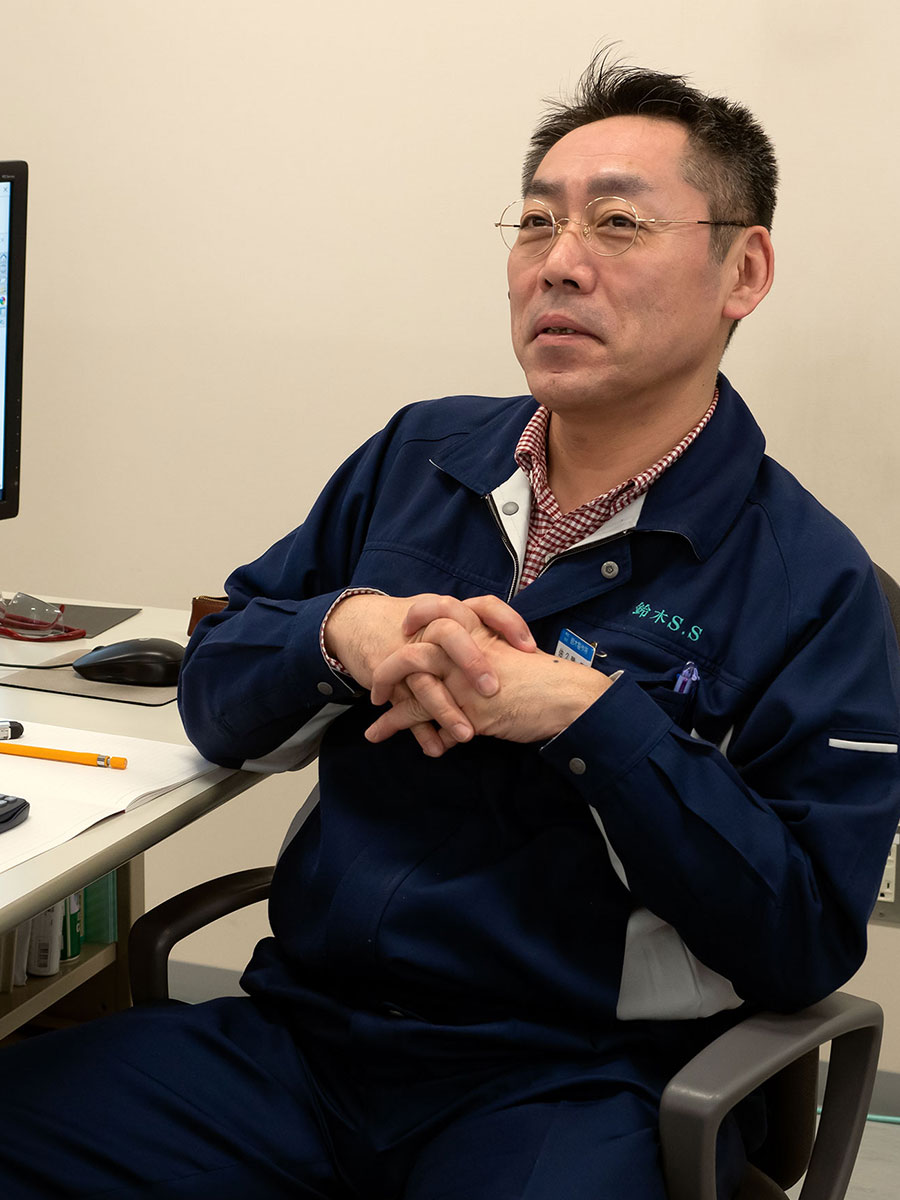
突如、山形に呼び戻されました
うちの父が鈴木製作所でエンジニアをずっとやってきていたのですが、私がちょうどアメリカ転勤の話が出たときに「あー、もう、すぐ帰って来い」と。「期限だ」って言ってました(笑)。まぁある意味理不尽極まりないのですが(笑)、父の話は沢山聞いてきていたので、鈴木製作所がどういう会社かという事もそれなりに理解していましたし、入ってもいいかなと。
開発はあくまでも自分でレールをひいて進んでいくしかないし、何をやるかは自分で探さなくちゃならないというような気持ちでしたし。誰かが責任を取ってくれるような規模の企業でもないので自由と責任は紙一重で、つまり、「本当にこれはお客様に喜ばれることなのだろうか?」とか、そういう迷いとかは常にあります。なので、あちこち出ていって、ベビーロック社さんがやっている講習会とかそういうところに行って、どんなふうなことに潜在的に困っていることは何かなってよく見てきたりなんかして、「あー、次はこれをやろう」とか、とにかく自分でやることを探して見つけて・・・と、ここ何年かこんなスタイルでやっています。
カルチャーショックもそれなりに
最も驚いたのは、やりたいと思ったことは、なんでも「はいどうぞやってください」ということでした。私が入社した頃ちょうど自動糸調子という初のシステムが出来上がっていて、ところがそれが凄い高コストで、部品調達も困っていて、しばしば欠品や入荷遅れが発生するし、これはさすがにまずいと思った。それを一気にコストダウンさせるためにガラッと設計変更しちゃってコストを下げたことが、誰からも言われなかったのですが私が最初に取り組んだ大きな仕事でした。
その次は、その当時生産ラインで驚くほど不良が出ていたのですが、歩留まりが本当に低くて、検品でそのまま合格して箱に入るものって10%あっただろうかくらいひどい時期もありました。
部品の諸要件が「未」共通理解
製品開発側も製造側も、発生している症状からその要因となり得る部品の要件とか、要素として関連することを全部リンクさせて想定して1件ずつ潰していくような不具合対策をしていきました。その当時の私は開発の担当だったので、当時の社長(今の社長のお父様)から「開発なのに何やっているんだ!」と最初は青筋立てて怒られまして(笑)。「そんなこと言ったって社長、このまま歩留まりが低かったらこの会社潰れます!」と言い返して、「私にやらせてくれ」と言って不具合対策を始めて今に至っています。
でも、その影響で僕はミシンの技術をすごい勉強させてもらったし、それがなかったら今の自分はなかったなと、振り返るとそう思います。
使ってくれている人がニコッと笑ってくれる
針糸通しもそうなのですが、もっと簡単に壊れない糸通しができないかということで取り組んでみたのがエアの糸通しです。針の糸通しで困っているお客さんが結構いて、修理だとか、針糸通しだけの修理で返ってきたりするものも結構多くて。交換部品なんかもかなりたくさん出ていたのです。最初うちの父にそう言ったら「できるわけねえだろそんなの、ばかじゃねぇか」って言われた(笑)。ところがどうして父がそれをやり始めちゃって、でもうまくいかなかった。その後に僕がやり始めて、まずはちょっと案があったので、その辺にあるものでちょっと適当に作ってみて、そうしたら針の穴にこれくらいの糸が通ったんです。「よし、これはいける」ということで本格的にやり始めて、必要要件をまとめて部下に設計してもらって、そして出来上がったのがエアの糸通しです。
やっぱり使っている方が、うちのミシンを使ってニコッと笑ってもらえるのが一番うれしいんです。それが僕らの明日への活力みたいなもので。
将来に向けた次の柱
将来お客様に喜んでもらえるもの、選んでもらえるものを作れていけたらいいなと自分は思っています。どんな方面かというと、これはまだ全く僕の個人の考えでしかないのですが、弊社の製品は今まで女性の方々に使って喜んでもらえるものを作ってきました。全く畑違いなものになるのかは分かりませんが、技術的にも多少近いところで、そういった女性の方々に喜んでもらえるようなものを生み出せると良いのかな・・・と大まかには思っています。
弊社のロックミシンや刺子ミシンという製品は趣味の道具なので、案外20~30年ほど経っても残っている可能性は高いと思いますが、もちろんその保証はない。もちろん簡単ではありませんが、包装機に続くもう一本の柱みたいなものを見つけたいなと日々思っています。社長からも「どんどんあっちこっち行ってネタ探してきて」と言っていただいています。
そしてやはり、誰かのために作る
今後どんどんITが進んでいって「人の心」というものがどんなふうに変化していくのか、世の中の在り方とかがどんなふうに変わっていくのかは分からないですけれども、ホッと一息つけるようなものであったり世界であったり、そういうものにお手伝いできるようなものを見つけられたらいいなって個人的には思っています。やはり、個人のそういう思いの集合体が会社というものでもありますし、実現のための1つのきっかけかもしれないなとどこかで信じているかも知れませんが、その先の想いとしては、やはり、「喜んでくれる誰か」のために作っていきたいという事だと思います。
ある日の佐久間さん
7:15 | 出勤 デスクで技術関連の書籍などを読む |
8:20 | 朝礼 |
8:30 | 経済や業界関連の新聞に目を通す |
9:00 | 三次元CADで設計業務 |
10:10 | アメリカの取引先とのテレビ会議に出席 開発中の製品に付いて意見交換をする |
12:00 | 昼食は持参した弁当を食べる 食後は読書をして過ごす |
13:00 | 関連部署との定例会議 所属の垣根を越えて課題に取り組む |
14:00 | 部下の業務の進捗確認 課題を抱えている様であればアドバイスをする |
17:00 | 1日の仕事をまとめる |
18:30 | 清掃や後片付けを終えて退勤 |
19:00 | 帰宅後は家族とゆっくり過ごす |
※実際の業務から内容を抽出して再構成しています。