成長を実感する機会と
新しい事への挑戦
-生産課 係長 五十嵐
高い品質と安定した供給は製造業として基本。
生産課の題意線で活躍する五十嵐さんの入社時のエピソードなどをご紹介します。
鈴木製作所と出会ったきっかけは偶然のインターン
私は山形県の産技短(山形県立産業技術短期大学校)を卒業して入社したのですが、きっかけはインターンシップで鈴木製作所に来たことです。
元々出身も山形市内で、もし近くで良い就職先があればいいなとはなんとなく考えていたのですが、自社製品をもち、企画・設計はもちろん、加工や組立などの製造までも一貫して山形の自社内でやっていて、さらにその製品が世界市場でのトップシェアを獲得しているという会社は決して多くはありません。私は部品の加工が好きなのでインターンで製造現場を見学できたことは大きかったですが、同時に会社の雰囲気を十分感じることができた事も大きく影響したと思います。やりたいことと合致してしかも会社が近いという、これも縁かなと。
図面と設備と、もちろん現実的な点も
就職活動は結果的に3社ほど検討していたのですが、部品加工についても各社やり方が色々とあり、鈴木製作所ではその求められるレベルが高く、現場で図面を読み込みながらやっているというところは私にとって重要でした。また、社内での技能検定や様々な資格にも手当が付いたりするのも技術者として経験を積むうえで良いなと思いましたし、従業員が積極的に取り組んでいる社内業務の改善活動とかも興味を惹かれたことの一つでしたし、あとは、他より給料が良かった(笑)。
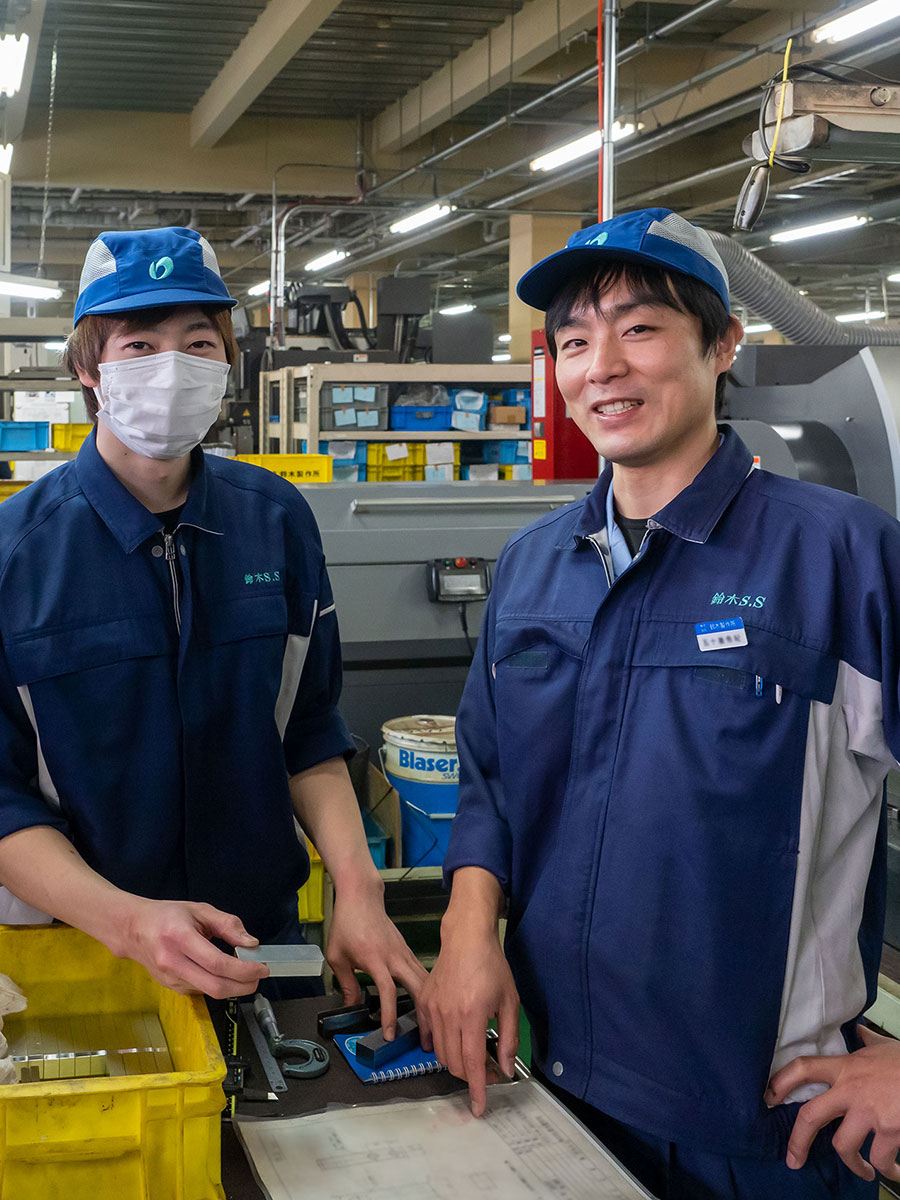
入社して最初の仕事は「手仕上げ」
弊社の製品に使われている部品でルーパーという部品がありまして、ルーパー室という専用の加工部屋があるのですが、そこでは手で削って部品を仕上げています。今は大きな加工機械を動かしていますが、入社して最初に担当した業務はその手仕上げの仕事で、途中で少々担当業務が変わったりもしましたが、それでも1年ほどだったと思います。
その後はずっと汎用機で、いわゆる旋盤やフライス盤とか使っての部品加工を5~6年ほど担当し、そのあとマシニングセンターを使い始めてもう8年ほど経つと思います。
成長を実感する機会、新しい事への挑戦
技能検定に合格したときは嬉しかったです。技術力を身に着けるために休日にも練習させてもらいましたし、当時のマキノ製の最新機種を最初に導入したメーカーでもあって、その立ち上げを任せてもらえたという事も嬉しかったです。今では私含めて10名ほどが使っていますが、マシニングの基本はフライス関係なので、それらの技術では誰にも負けたくないという気持ちはあります。
私が当時担当した部品が導入の対象だったという運もあると思いますが、技術的な成長もあっての事だと思います。また、新製品の立ち上げは挑戦なので楽しいです。自分の加工プログラムが採用されたり、もちろん部品は新設計で、加工を決めていくことは挑戦ですし、失敗する訳にはいきません。
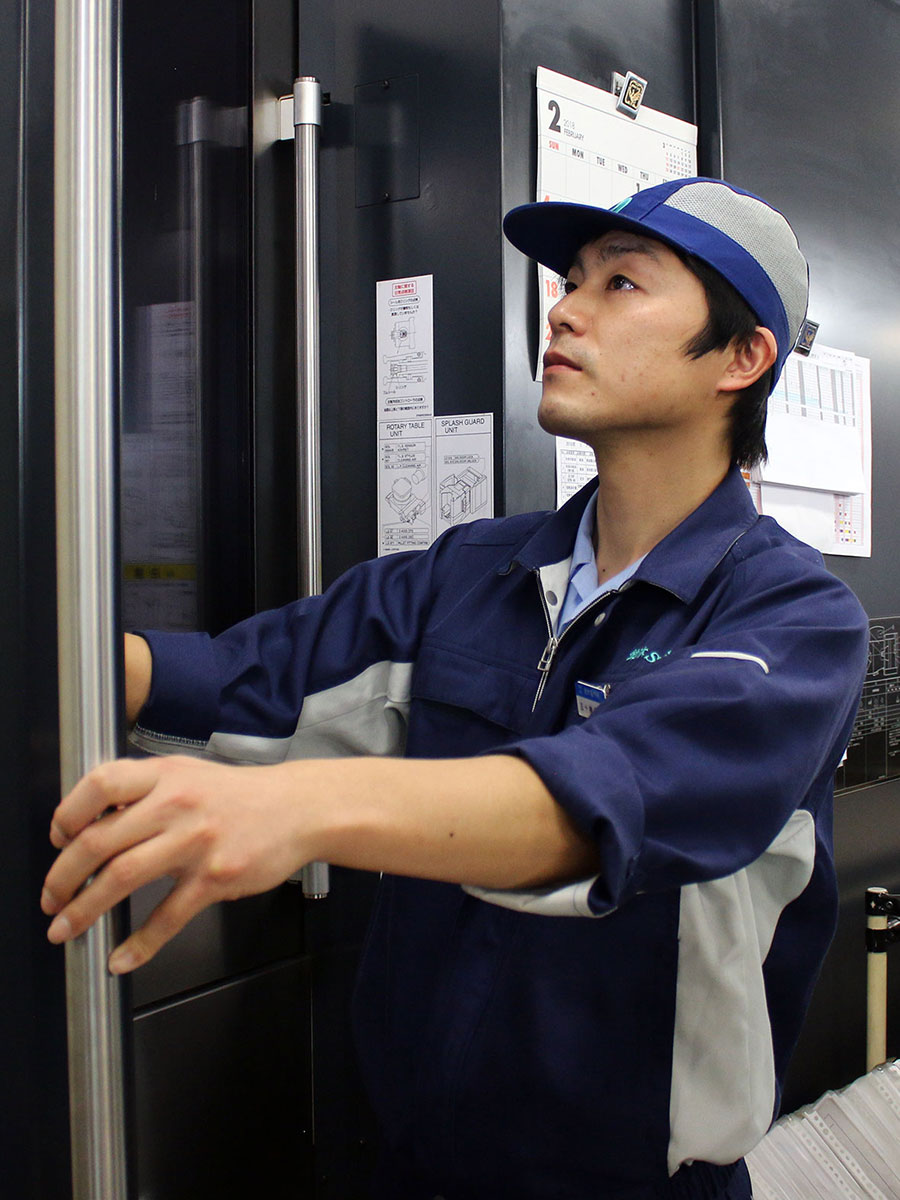
いかに工程削減して簡単に製造できるかが腕の見せ所
最近は「多パレット」のマシンが今横型増えていて、いかに簡単に加工するか、工程を減らせるか、そういうところは徹底的にこだわって取り組んでいます。今私が担当している部品は多品種少量加工がメインなので、多パレットとはいえ工具本数には制限がありますし、いかに本数を少なく共有化して、多くの多品種のものを加工するかにこだわっています。最初の頃は比較的加工するものが決まっていて、それに対してどう調整して加工するというので精いっぱいでした。でも今は図面をもらうと「材料何手配しようかな?」とか、工具選定や段取りはもちろんですが、自分でプログラムも組めて全部やれるので、5年前とは格段に違うと思います(笑)。
それでも数値化や機械化が難しい手仕上げ
手仕上げに関して言えば、特殊な形状をしている磨き部品などはやはりどうしても測れない。先端がどれくらいとかそういうのは測れるものの、ある一点の逃げの深さとか、数値でなかなか表わせないところを要求される仕事というのはやはりとても気を使いますし、「形状を出す」という事がまだまだ人間の見た目と感覚で評価せざるを得ないので本当に難しいです。完成品との照合であったり、熟練の戦敗から直接教えてもらったときの「感覚」であったり、実際に部品を組み込んで動かしてみて問題が無かいかを確認したり。最初の頃はその仕上がり具合が本当に大丈夫か心配したりもしましたが、そういう経験の積み重ねでしか乗り越えられない事もあります。それでも未だに「これで大丈夫かな?」と照らし合わせながら確認することは多くあります。
職人気質なベテランの先輩方からの救い
個人的に苦労したと思うのは、加工よりも主任とか係長になった時、やはりいろんな人との関わり方とか。もちろん難しい加工もありますが、だいたいは苦労しても解決することが多くあります。ただ、それでもどうしても難しいときはやっぱりあります。そういう時でもやはりベテランの人達がいるので、いろいろ聞きながらやれた事で加工については結果的にどうにかなってきたのだと思います。
あくまでも会社としての役割上ですが主力が若い世代に移されていった時に、いざそうは言ってもやり方が分からなかったりしたので、かなりいろいろと質問しながら乗り越えてきたと思います。エンジニアの世界って、私たちの世代とベテランの人達の世代では“教え方”や“教わり方”とか、職人気質みたいな習慣的な違いも相応にあったりもして、でも相談できるベテランがいるというのは救われてるなと思います。
ある日の五十嵐さん
7:30 | 自宅を出発 |
7:50 | 出勤 設備の暖機運転をして1日の準備をする |
8:20 |
朝礼 |
8:40 | 昨日完成した部品の納品確認、本日の注文部品の確認をして1日のスケジュールを組み立てる |
9:00 | 加工部品の検査 刃具の交換や寸法調整をする |
11:00 | 購買課へ材料の注文、同僚へ関連部品の加工依頼 |
12:00 | 食堂で昼食 |
13:00 | 生産課内での会議に参加 |
13:30 | マシニングセンタでの部品加工 |
16:30 | 後工程へ完成部品の納品 |
17:20 | 部品加工を継続して残りの部品を仕上げる |
19:30 | 清掃や後片付けをして退勤 |
20:00 | 帰宅 家族との時間を過ごす |
※実際の業務から内容を抽出して再構成しています。